Hwashin Bolt Industries actively responds to evolving customer needs and continuously conducts R&D on special materials and uniquely shaped bolts.
R&D Center Research Institute
Analysis
Material Research and Analysis
Development
R & D of precise material processability
Perform
Government R & D Research Projects
Link Project
Hwashin Bolt Industries is engaged in field application technology development, innovative talent training, and joint research through industry-academia collaboration projects.
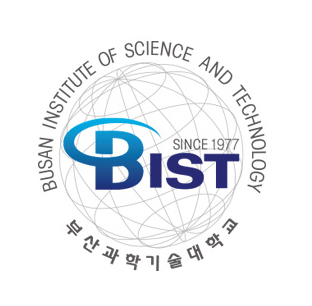
BUSAN INSTITUTE OF SCIENCE AND TECHNOLOGY
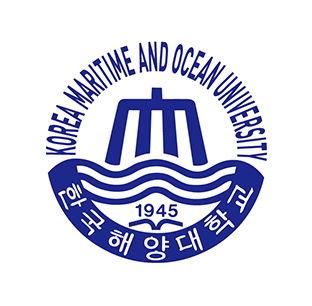
KOREA MARITIME AND OCEAN UNIVERSITY
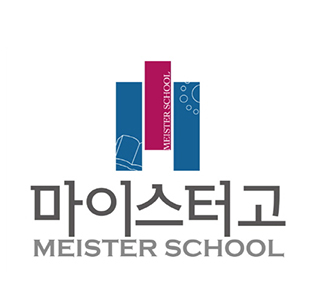
BUSAN AUTOMOTIVE HIGH SCHOOL
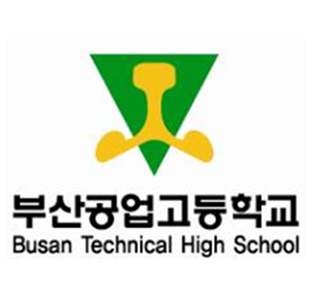
BUSAN TECHNICAL HIGH SCHOOL
R&D Project
Hwashin Bolt Industries is conducting research and development projects aimed at developing new products and enhancing productivity to meet diverse customer needs and evolving environmental changes.
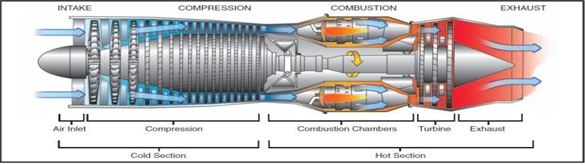
– Developed Product : Compressor Rotor Bolt.
A critical component that penetrates and secures a high-temperature, high-speed rotating compressor disk.
One of the most valuable high-value-added components in turbine systems.
- Importance of Stability and Quality
- Stability and quality are essential in compressor rotor bolts.
- Customer quality requirements are extremely strict to ensure safety and performance.
- Precision Machining Technology
- Advanced precision machining is required for hard metal processing.
- Ensures high durability and precise fit for demanding turbine applications.
- Long-Axis Concentricity & Straightness Control
- High concentricity and straightness control are crucial for optimal rotor performance.
- Minimizes vibration and misalignment during high-speed rotation.
- Surface Treatment & Quality Inspection
- Specialized surface treatment technologies enhance durability and resistance.
- Comprehensive quality inspection processes ensure compliance with strict industry standards.
Split Mechanical Seal
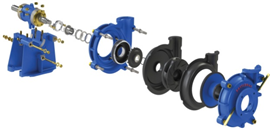
Existing Mechanical Seal
- Assemble the perturbation part on the rotating shaft in the axial direction
- Disassemble the entire rotating device when replacing after a certain period of use.
- Increase maintenance time / cost
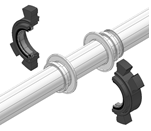
Separate Mechanical Seal
- Pivoting parts on the rotating shaft are assembled from both sides
- Easily disassembled and assembled when replacing (Maintenance time, cost reduction)
Excellence and differentiation of development technology
No need to disassemble the entire pump for mechanical seal replacement.
Replacement time: 10 ~ 12 hours -> 1 hour
More than 90% cost savings